2-11
decreased, the error signal would increase in amplitude and cause the motor to speed up. In the same way,
if the antenna were to speed up, the tach output would increase, decreasing the error signal and the motor
would slow down. Without the velocity loop to compensate for changing conditions, the load could not
respond in the desired manner.
The system shown in figure 2-7 is a simplified version of a velocity loop. In practice, the reaction of
the motor to error voltage and the output of the tach would not be equal (10 rpm per volt and 1 volt per 10
rpm). This would be compensated for by gearing between the motor and load and between the load and
tach, or by using a summation network in which the resistors (R2 and R3) are riot equal. This use of
unequal resistors is called a SCALING FACTOR and compensates for tach outputs and required motor
inputs. This is just another way of saying that the individual components of the velocity loop must be
made to work together so that each can respond in a manner that produces the desired system result.
Q-9. What are two major differences between velocity servos and position servos?
Q-10. In a typical velocity servo block diagram what device is placed in the feedback loop that is not
present in the position servo?
Q-11. What is the advantage of using a closed-servo loop to control load velocity?
The Acceleration Servo
The acceleration servo is similar to the two loops we just discussed except that the acceleration of the
load is sensed, rather than the position or velocity. In this loop, the tachometer of the velocity loop is
replaced by an accelerometer (a device that generates a signal in response to an acceleration) as the
feedback device.
We have not provided an illustration of the acceleration servo because of the complexity of its
applications as well as its components. This type of servo is widely used in the rocket and missile fields,
and is used whenever acceleration control is required.
SERVO CHARACTERISTICS
Servo characteristics vary primarily with the job the servo is designed to do. There are almost as
many types of servos as there are jobs for servos. All servos usually have the common purpose of
controlling output in a way ordered by the input. Ideally, motion and output shaft position should
duplicate the track of the input shaft. However, this ideal performance is never achieved. We will discuss
the major reasons for this, and show some methods used in the attempt to approach the ideal.
Because a servo compares an input signal with a feedback response, there will always be a TIME
LAG between the input signal and the actual movement of the load. Also, the weight of the load may
introduce an additional time lag. The time lag of the servo can be decreased by increasing the gain of the
servo amplifier. If the gain is set too high, however, the servo output will tend to oscillate and be unstable.
From this you can see that the gain of a servo is limited by stability considerations. Servo sensitivity must
be considered along with stability to reach a "happy medium."
TIME LAG
To reduce time lag, the gain of the servo amplifier could be increased. Increasing the gain of the
servo amplifier will decrease the lag time and cause the load to move faster. However, there is a serious
drawback because the load is moving faster, its inertia will likely cause it to go past the desired position
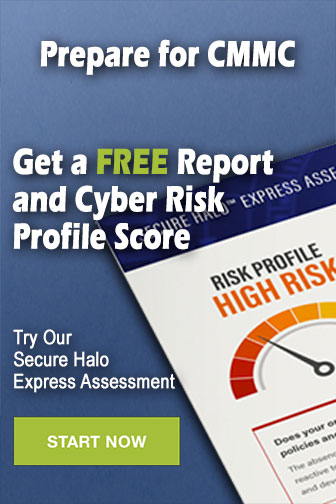