2-10
Figure 2-7.Block diagram of a velocity servo.
In this application, the tach is used as a feedback device and is designed to produce 1 volt of
feedback for each 10 rpm.
Let's assume that the motor is designed to turn 10 rpm for each volt of error signal. Figure 2-7 shows
the tach mechanically connected to the load. With this arrangement, the shaft of the tach rotates as the
load rotates, and the tach can be said to "sense" the speed of rotation of the load. For purposes of
explanation, we win assume that the load is an antenna that we want to rotate at 30 rpm.
Initially, the wiper arm of R1 is set at the 0-volt point (mid-position). This applies 0 volts to the left
side of R
2. Since the motor is not turning, the load is not being driven, and the tach output is 0 volts. This
applies 0 volts to the left side of R
3. Under these conditions, 0 volts is felt at the sum point and the motor
is not driven. The voltage at the sum point is the error signal. When the wiper arm of R1 is moved to the
-9 volt point, an error signal appears at the sum point. At the first instant, the error signal (at the sum
point) is -4.5 volts. This is because, at the first instant, the load and tach have not started to move. With
the tach output at 0 volts, and the wiper of R1 at -9 volts, -4.5 volts is present at the sum point. This
voltage will cause the motor to start to rotate the load.
After a period of time, the load (and tach) are rotating at 10 rpm. This causes the tach to have an
output of +1 volt. With +1 volt from the tach applied to the bottom of R3, and -9 volts (from R1 wiper)
applied to the top of R2, the voltage at the sum point (error signal) is -4 volts. Since the motor will turn 10
rpm for each volt of error signal, the motor continues to speed up. When the load reaches 30 rpm, the tach
output is +3 volts. With this +3 volts at the bottom of R3 and the -9 volts at the top of R
2, the error signal
at the sum point is -3 volts. This -3 volts is the voltage required to drive the motor at 30 rpm, and places
the system in balance. This satisfies the two conditions of the velocity servo. (1) The velocity of the
output is sensed (by the tach), and (2) an error signal (-3 volts) is still present and the load continues to
move when the velocity loop is at correspondence (30 rpm).
You may ask why the velocity loop and feedback are necessary. If this motor turns 10 rpm for each 1
volt error signal, why not simply feed -3 volts into this amplifier from the wiper of R1 and not have a tach
or summing network?
The answer is that the velocity loop will regulate the speed of the load for changing conditions. If the
load in figure 2-7 were a rotating antenna on a ship, the antenna would tend to slow down as the wind
opposed its movement and speed up as the wind aided its movement. Whenever the antenna slowed
down, the output of the tach would decrease (since the tach is connected to the load). If the tach output
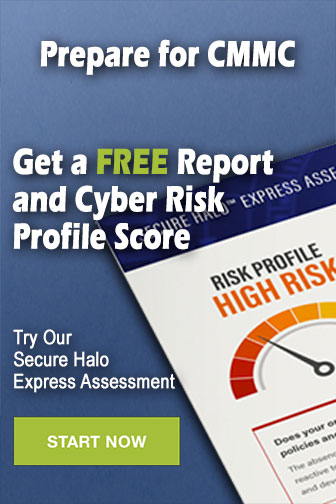