2-13
Friction Clutch Damping
The friction clutch damper uses a friction clutch to couple a weighted flywheel to the output drive
shaft of the servo motor. As the servo motor rotates, the clutch couples some of this motion to the
flywheel. As the flywheel overcomes inertia and gains speed, it approaches the motor speed. The
flywheel, in turning, absorbs energy (power) from the servo motor. The amount of energy stored in the
flywheel is determined by its speed (velocity). Because of inertia, the flywheel resists any attempt to
change its velocity.
As the correspondence point of the system is approached, the error signal is reduced and the motor
begins to slow down. In an attempt to keep the output shaft turning at the same speed, the flywheel
releases some of its energy into the shaft. This causes the first overshoot to be large. When the servo
system drives past the point of correspondence, a new error signal is developed. The new error signal is of
opposite polarity and causes the servo system motor to drive in the opposite direction. Once again the
flywheel resists the motor movement and absorbs energy from the system. This causes a large reduction
in the second overshoot and all subsequent overshoots of the system. The overall effect is to dampen the
oscillations about the point of correspondence and reduce the synchronizing time.
The motor rotation is transmitted to the flywheel through the friction clutch. The inertia of the
flywheel acts as an additional load on the motor. The friction clutch is designed to slip with a rapid
change of direction or speed. This slipping effectively disconnects the flywheel instantaneously, and thus
governs the amount of power the flywheel draws from the motor.
Magnetic Clutch
Another type of damper is the MAGNETIC CLUTCH. This type is similar in function to the friction-
clutch damper. The main difference between the two is the method used to couple the flywheel to the
shaft of the servo motor. There are two distinct types of magnetic clutch dampers. The first uses a
magnetic field to draw two friction clutch plates together to produce damping. The action is similar to the
friction clutch we just described.
The second version of the magnetic clutch uses the action of a magnetic field generated by two sets
of coils, or one set of coils and the induced eddy currents, which result from rotation of the single set of
coils near a conducting surface (the flywheel).
Coupling in this type of clutch is made by the interaction of two magnetic fields without a physical
contact between the two. The two-coil or eddy-current type of magnetic clutch offers smoother operation
than a pure friction clutch and has no problem of wear because of friction.
In summary, a smooth, efficient operating servo system can only be achieved by a system of
compromises. As you recall, earlier we increased the gain of the amplifier to reduce time lag. This had the
drawback of increasing hunting or oscillations about the point of correspondence. We overcame this
difficulty through friction damping. This solved the problem of hunting and smoothed out servo operation
but acted as part of the servo load. It caused a large first overshoot and increased the time lag. Some form
of damping that can be used with high amplification to obtain smooth servo operation and minimum time
lag is needed. The answer lies with the use of ERROR-RATE damping.
Q-14. Why is damping needed in a practical servo system?
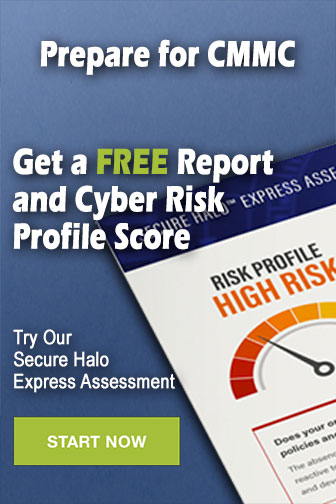