2-26
diodes are cut off, and zero potential is felt across the output terminals. The circuit will remain in this
condition until an ac error signal is applied. As we make this circuit work, you will notice that CR1 will
conduct when the input signal is in phase with the reference voltage and then only on the positive half-
cycle. CR2 will remain in cutoff unless the phase relationship between the ac error signal and the
reference voltage changes by 180º. At this time CR1 will cut off. This change could be brought about by
the error detector in the servo system sensing a change in the direction of the load. Effectively, we have a
one-diode circuit for one direction of rotation.
Assume that an ac error signal is applied to T2, making the anode of CR1 positive and the anode of
CR
2
negative. At the same time, the reference voltage on the anodes of CR1 and CR2 is on its positive
half-cycle. Under these conditions, CR1 will conduct and CR2 will be cut off. A positive voltage will be
developed across Ri and felt on the output terminals. During the negative half-cycle, a negative voltage
will be felt on the anodes of CR1, and CR2 and will cut them off. The output of the circuit for one
complete cycle of the reference signal will be a filtered, pulsating, dc voltage. As long as the input and
reference signals are in phase, the circuit acts as a half-wave rectifier and a filter network.
As we mentioned earlier, this circuit will also respond to a 180º phase reversal between the input and
reference signals. For instance, when the error signal applied to T2 is 180º out of phase with the reference
signal, CR2 conducts and CR
1
cuts off, causing the output voltage to change polarity. You may encounter
variations of the diode phase detector; however, they all depend on the same basic principle of operation.
To quickly summarize, the demodulator converted the ac input signal to a dc error signal. The
polarity of the dc error signal was determined by the phase relationship between the ac error input signal
and the reference signal. The amplitude of the dc error signal was directly proportional to the magnitude
of the ac input signal.
Q-23. What is the purpose of a demodulator in a servo system?
SERVO AMPLIFIERS
The servo amplifiers previously discussed were used in servo systems to amplify either the ac or dc
error signal to a sufficient amplitude to drive the servo motor. These amplifiers are the same amplifiers in
principle as covered in NEETS Module 8, Introduction to Amplifiers. The basic amplifier chosen for use
in the servo system must have the following characteristics:
1. Flat gain versus frequency response over the broad band of frequencies of interest.
2. Minimum phase shift with a change in input signal (zero phase shift is desired, but a small
amount of phase-shift is acceptable, if constant).
3. A low output impedance.
4. A low noise level.
Up to this point in our discussion of servos, the amplifiers have been directly connected to the motor
that drove the load. Servo amplifiers are also used within the system itself to amplify the error signal. For
example, the signal from the demodulator or filter network may require additional amplification to
maintain signal strength. In cases where the amplifier is used to feed large drive motors, to move large
loads, the basic electronic amplifier that was presented earlier in this training series is not adequate to do
the job. This type of work is done by large power amplifying devices such as the amplidyne generator
(NEETS, Module 5, Introduction to Generators and Motors) and the MAGNETIC AMPLIFIER, which
we will discuss later in this chapter.
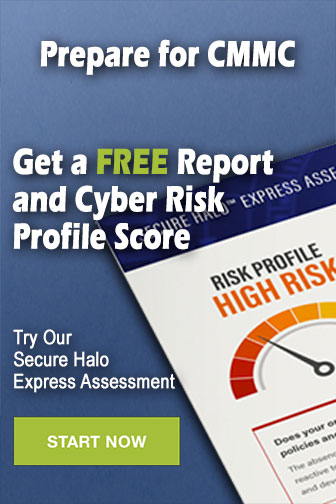