2-27
AC SERVO MOTORS
Large ac motors are too inefficient for servo use. To move large loads, the ac motor draws excessive
amounts of power, and is difficult to cool. Hence, ac servo motors are used primarily to move light loads.
Most of the ac servo motors are of the two-phase or split-phase induction type. Fundamentally, these
motors are constant-speed devices, although their speeds can be varied within limits by varying the
amplitude of the voltage to one of the motors stator windings. When the load becomes heavy, the
workhorse dc servo motor is used.
DC SERVO MOTORS
The control characteristics of dc servo motors are superior to those of ac servo motors. The dc servo
motor can control heavy loads at variable speeds. Most dc servo motors are either the permanent magnet
type, which are used for light loads, or the shunt field type, which are used for heavy loads. The direction
and speed of the dc motor's rotation is determined by the armature current. An increase in armature
current will increase the motor's speed. A reversal of the motor's armature current will change the motor's
direction of rotation More thorough explanations of ac and dc motors are given in NEETS Module 5,
Introduction to Generators and Motors.
SYNCHRONIZING CIRCUITS
As we explained in chapter 1, the use of a multi-speed synchro transmission system increases the
accuracy of data transmission. The accuracy of the servo system depends in part upon the accuracy of the
input fed from the synchro system. For example, a dual-speed synchro system operating in conjunction
with a servo system uses two CTs (one coarse and one fine) to define a quantity accurately. This is done
by feeding the output of the COARSE CT to the servo amplifier when the system is far out of
correspondence and then shifting to the output of the FINE CT when the system is within 2 or 3 degrees
of synchronization. A circuit that will perform this job is known as a SYNCHRONIZING NETWORK.
A synchronizing network (also called a crossover or switching network) senses how far the servo
load is from the ordered position and then switches either the coarse signal or the fine signal into control.
The signal selected by the circuit is the input to the amplifier. The selection is based on the size of the
error signals the circuit receives. The coarse signal is the predominant factor in the selection, since it is a
measure of the servo's output position throughout its limit of motion. The coarse signal drives the system
into approximate synchronization, and then the fine signal is shifted into control.
Semiconductor-Diode Synchronizing Network
The SEMICONDUCTOR-DIODE SYNCHRONIZING NETWORK is fairly common and typical of
the type used in servo systems. Let's take a look at a circuit that uses this technique. Figure 2-19 is an
illustration of the circuit. In the following explanation, we will assume that the system is far out of
correspondence (more than 3º). At this time, the coarse signal is large in amplitute. With this condition,
CR
3
and CR4, or CR5 and CR6, will be forward-biased, depending upon the polarity of the input signal.
This will cause current to flow through R1. The voltage developed across R1 is felt on one leg of the
summing newtork. A large amplitude fine signal CANNOT be present in the summing network, because
CR1 and CR
2
are designed to limit the fine amplitude to a small value. With this condition present at the
summing network, the coarse signal maintains control and drives the load toward correspondence.
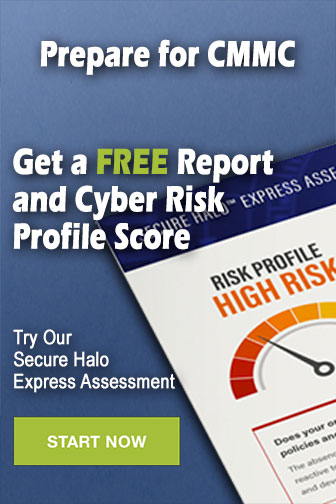