5-28
Figure 5-24.Pulse generator selector chart.
Next, the technician needs to select the polarity of the output desired by using the positive (+) and/or
negative (-) push buttons. All three buttons only function in a push-on/push-off mode and will only
interact with each other to avoid the NOT ALLOWED state found in figure 5-24.
Once the specific output type has been selected, the output desired by the technician is set using the
LEVEL and WIDTH controls. The LEVEL control is used to vary the magnitude of the output amplitude
from zero to 5 volts (peak or DC). During the PULSE mode, the WIDTH control will adjust the cycle of
the pulse output from low to 50 percent maximum (square wave).
The start of a pulse will be triggered by the appropriate zero crossing of the test signal, which results
in the pulse frequency being equal to the selected test signal frequency.
The end of the pulse is determined by the WIDTH control setting, which determines the cycle length.
The WIDTH control, however, has no effect when the DC mode is selected.
FUNCTIONAL OVERVIEW
There are six major sections in the Tracker 2000, as shown in the block diagram in figure 5-25. The
control logic section controls the selection of the channel, frequency, impedance range, and pulse
generator mode according to the front-panel buttons pushed by the technician. The oscillator provides the
test signal that is used by the signal and pulse generator sections. In the signal section, the test jacks are
driven by the test signal, while signal conditioners monitor the jacks and produce the horizontal and
vertical signals used by the CRT section to produce a component signature on the display. The pulse
generator provides an added source for testing three additional terminal devices. The power supply
produces all the required voltages needed to operate the Tracker 2000.
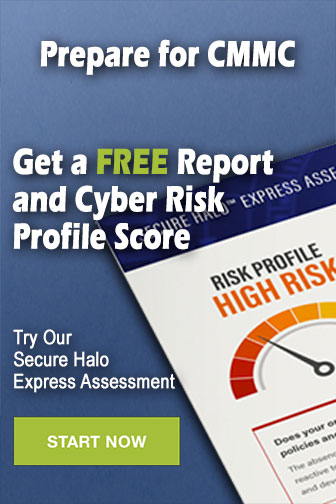