3-23
Q18. In what direction are component leads clinched on single- and double-sided boards?
Soldering of PCB Components
The fundamental principles of solder application must be understood and observed to ensure
consistent and satisfactory results. As discussed in topic 2, the soldering process involves a metal-solvent
action that joins two metals by dissolving a small amount of the metals at their point of contact.
SOLDERABILITY.As the solder interacts with the base metals, a good metallurgical bond is
obtained and metallic continuity is established. This continuity is good for electrical and heat conductivity
as well as for strength. Solderability measures the ease with which molten solder wets the surfaces of the
metals being joined. WETTING means the molten solder leaves a continuous permanent film on the metal
surface. Wetting can only be done properly on a clean surface. All dirt and grease must be removed and
no oxide layer must exist on the metal surface. Using abrasives and/or flux to remove these contaminants
produces highly solderable surfaces.
HEAT SOURCE.The soldering process requires sufficient heat to produce alloy- or metal-solvent
action. Heat sources include CONDUCTIVE, RESISTIVE, CONVECTIVE, and RADIANT types. The
type of heat source most commonly used is the conductive-type soldering iron. Delicate electronic
assemblies require that the thermal characteristics of a soldering iron be carefully balanced and that the
iron and tip be properly matched to the job. Successful soldering depends on the combination of the iron
tip temperature, the capacity of the iron to sustain temperature, the time of iron contact with the joint, and
the relative mass and heat transfer characteristics of the object being soldered.
SELECTION OF PROPER TIP.The amount of heat and how it is controlled are critical factors
to the soldering process. The tip of the soldering iron transfers heat from the iron to the work. The shape
and size of the tip are mainly determined by the type of work to be performed. The tip size and the
wattage of the element must be capable of rapidly heating the mass to the melting temperature of solder.
After the proper tip is selected and attached to the iron, the operator may control the heat by using
the variable-voltage control. The most efficient soldering temperature is approximately 550 degrees
Fahrenheit. Ideally, the joint should be brought to this temperature rapidly and held there for a short
period of time. In most cases the soldering action should be completed within 2 or 3 seconds. When
soldering a small-mass connection, control the heat by decreasing the size of the tip.
Before heat is applied to solder the joint, a thermal shunt is attached to sensitive component leads
(diodes, transistors, and ICs). A thermal shunt is used to conduct heat away from the component. Because
of its large heat content and high thermal conductivity, copper is usually used to make thermal shunts.
Aluminum also has good conductivity but a smaller heat content; it is also used to conduct heat,
especially if damage from the physical weight of the clamp is possible. Many types, shapes, and sizes of
thermal shunts are available. The most commonly used is the clamp design; this is a spring clip (similar to
an alligator clip) that easily fastens onto the part lead, as shown in figure 3-16.
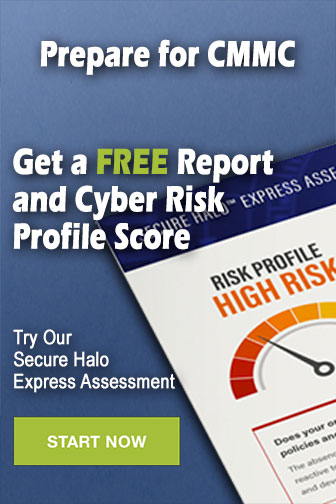