3-26
Removal of Plug-In DIPs
To remove plug in DIPs, use an approved DIP puller, such as the one shown in figure 3-18. The
puller shown is a plastic device that slips over the ends of the DIP and lifts the DIP evenly out of the
socket. Before the DIP is removed, the board is marked or a sketch is made of the DIP reference mark
location; then the reference mark for the replacement part will be in the proper position. The DIP is
grasped with the puller and gently lifted straight out of the socket. Lifting one side or one end first results
in bent leads. If the removed DIP is to be placed back in the circuit, particular care is taken in
straightening bent leads to prevent breaking. To straighten bent leads, the technician grasps the wide
portion of the lead with one pair of smooth-jaw needle nose pliers; with another pair, the technician then
bends the lead into alignment with the other leads. Tools used for lead straightening should be cleaned
with solvent to remove contaminants.
Figure 3-18.Typical DIP puller.
To replace a plug-in DIP, the technician should clean the leads with solvent and then check the
proper positioning of the reference mark. To do this, the technician holds the DIP body between the
thumb and forefinger and places the part on the socket to check pin alignment. The pins are not touched.
If all pins are properly aligned, the technician presses the part gently into the socket until the part is firmly
seated. As pressure is applied, each pin is checked to ensure that all pins are going into the socket. If pins
tend to bend, the part is removed and the pins are straightened. The socket is then inspected to make sure
the holes are not obstructed. Then the process is repeated. After a thorough visual inspection, the card
should be ready for testing.
Removal and Replacement of Soldered-In DIPs
The removal of soldered-in DIPs without conformal coatings is essentially the same as the removal
of discrete components, except that a skipping pattern is always used. A skipping pattern is one that skips
from pad to pad, never heating two pads next to each other. This reduces heat accumulation and reduces
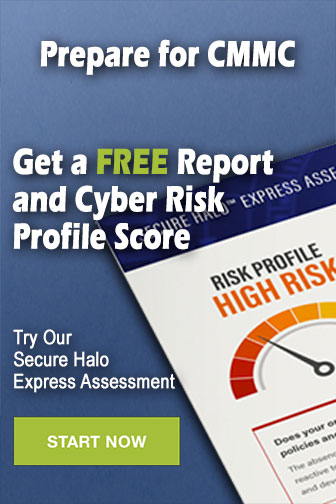