3-27
the chance of damage to the board. Of course, many more leads should be desoldered before the part can
be removed. Special care must be exercised to make sure all leads are completely free before an attempt is
made to lift the part off the board. If the part is known to be faulty, or if normal removal may damage the
board, then the leads should be clipped. Once this has been done, desoldering can be done from both sides
of the board. After the clipped leads have been desoldered, they can be removed with tweezers or pliers.
The removal of DIPs from boards with conformal coatings should be completed in the same manner
as for other components. The coating should be removed using the preferred method of removal for that
particular type of material. The coating should be removed from both sides of the board after masking off
the work area. Particular care should be taken when removing the material from around the delicate leads.
If the part is to be reused, as much of the coating should be removed from the leads as possible. As with
DIPs without conformal coatings, if the part is known to be bad or if the possibility of board damage
exists, the leads are clipped; the part and leads are then removed as described earlier in this section. Once
the part has been removed, the work area should be completely cleaned to remove any remaining coating
or solder.
The steps for replacing a soldered-in DIP are similar to those for replacing a plug-in DIP. Once the
part is in position, it is soldered using the same standard used by the manufacturer, or as close to that
standard as is possible with the available equipment. The joints should be soldered as quickly as possible
using only as much heat as is necessary using a skipping pattern. The repaired card should then be
visually inspected for defects in workmanship, and testing of the card should take place. Once the
successful repair has been accomplished, a conformal coating should be applied to the work area.
REMOVAL AND REPLACEMENT OF TO PACKAGES
You should recall from chapter 1 of this module, that TO packages are mounted in two ways
plugged-in or embedded. The term plug-in, when referring to TOs, should not be confused with DIP
plug-ins. TOs are normally soldered in place. You will come across sockets for TOs, but not as frequently
as for DIPs. Figure 3-19 shows the methods of mounting TOs. Notice that plug-ins may either be
mounted flush with the board surface or above the surface with or without a spacer. The air gap or spacer
may be used by the manufacturer for a particular purpose. This type of mounting could be used for heat
dissipation, short circuit protection, or to limit parasitic interaction between components. The spacer also
provides additional physical support for the TO. The technician is responsible for using the same
procedure as the manufacturer to replace TOs or any other components.
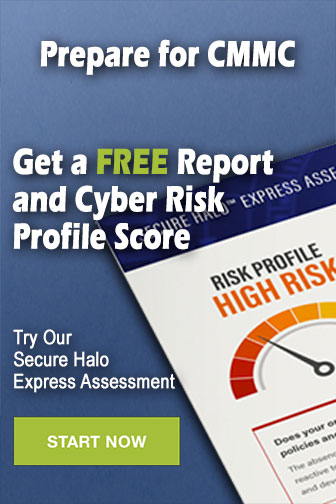