3-19
the delicate pad. This method is seldom used because it is not effective in preventing sweating of the lead
to the hole nor for cooling the workpiece.
Hot-Air Jet Method.The hot-air jet method uses pressure-controlled, heated air to transfer heat to
the solder joint without physical contact from a solder iron. This permits the reflow of delicate joints
while minimizing mechanical damage.
When the solder is removed from the lead and pad area, the technician can observe the actual
condition of the lead contact to the pad area and the amount of the remaining solder joint. From these
observed conditions, the technician can then determine a method of removing the component and lead.
With straight-through terminations, the component and lead may be lifted gently from uncoated
boards with pliers or tweezers. Working with clinched leads on uncoated boards requires that all sweat
joints be removed and that the leads be unclinched before removal.
The techniques that have been described represent the successful methods of desoldering
components. As mentioned at the beginning of this section, the 2M technician must decide which method
is best suited for the type of solder joint. Two commonly used but unacceptable methods of solder
removal are heat-and-shake and heat-and-pull methods.
In the heat-and-shake method, the solder joint is melted and then the molten solder is shaken from
the connection. In some cases, the shaking action may include striking the assembly against a surface to
shake the molten solder out of the joint. This method should NEVER be used because all the solder may
not be removed and the solder may splatter over other areas of the board. In addition, striking the board
against a surface can lead to broken boards, damaged components, and lifted pads or conductors.
The heat-and-pull method uses a soldering iron or gang-heater blocks to melt individual or multiple
solder joints. The component leads are pulled when the solder is melted. This method has many
shortcomings because of potential damage and should NOT be attempted. Heating blocks are patterned to
suit specific configurations; but when used on multiple-lead connections, the joints may not be uniformly
heated. Uneven heating results in plated-through hole damage, pad delamination, or blistering. Damage
can also result when lead terminations are pulled through the board.
When desoldering is complete, the workpiece must undergo a careful physical inspection for damage
to the circuit board and the remaining components. The technician should also check the board for
scorching or charring caused by component failure. Sometimes MEASLING is present. Measling is the
appearance of light-colored spots. It is caused by small areas of fiberglass strands that have been damaged
by epoxy overcuring, heat, abrasion, or internal moisture. No cracks or breaks should be visible in the
board material. None of the remaining components should be cracked, broken, or show signs of
overheating. The solder joints should be of good quality and not covered by loose or splattered solder,
which may cause shorts. The technician should examine the board for nicked, cracked, lifted, or
delaminated conductors and lifted or delaminated pads.
Q10. When does most printed circuit board damage occur?
Q11. What procedure involves the use of finely braided copper wire to remove solder?
Q12. What is the most effective method of solder removal?
Q13. When, if at all, should the heat-and-shake or the heat-and-pull methods of solder removal be
used?
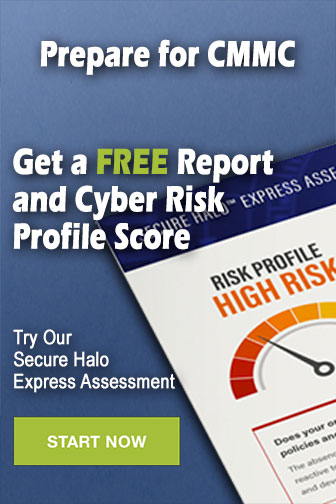