3-20
INSTALLATION AND SOLDERING OF PRINTED CIRCUIT COMPONENTS
The 2M technician should restore the electronic assembly at least to the original manufacturer's
standards. Parts should always be remounted or reassembled in the same position and with termination
methods used by the original manufacturer. This approach ensures a continuation of the original
reliability of the system.
High reliability connections require thoroughly cleaned surfaces, proper component lead formation
and termination, and appropriate placement of components on the board. The following paragraphs
describe the procedures for properly installing components on a board including the soldering of these
components.
Termination Area Preparation
The termination areas on the board and the component leads are thoroughly cleaned to remove oxide,
old solder, and other contaminants. Old or excess solder is removed by one of the desoldering techniques
explained earlier in this topic. A fine abrasive, such as an oil-free typewriter eraser, is used to remove
oxides. This is not necessary if the area has just been desoldered. All areas to be soldered are cleaned with
a solvent and then dried with a lint-free tissue to remove cleaning residue.
Component Lead Preparation
Component leads are formed before installation. Both machine- and hand-forming methods are used
to form the leads. Improper lead formation causes many repairs to be unacceptable. Damage to the
SEALS (point where lead enters the body of the component) occurs easily during the forming process and
results in component failure. Consequently, lead-forming procedures have been established. To control
the lead-forming operation and ensure conformity and quality of repairs, the technician should ensure the
following:
1. The component is centered between the holes, and component leads are formed with proper
bend-radii and body seal-to-bend distance.
2. The possibility of straining component body seals during lead forming is eliminated.
3. Stress relief loops are formed without straining component seals while at the same time
providing the desired lead-to-lead distances.
4. Leads are measured and formed for both horizontal and vertical component mounting.
5. Transistor leads are formed to suit standard hole spacing.
Lead-Forming Specifications.
Component leads are formed to provide proper lead spacing.
The minimum distance between the seal (where the lead enters the body of the component) and
the start of the lead bend must be no less than twice the diameter of the lead, as shown in figure
3-13.
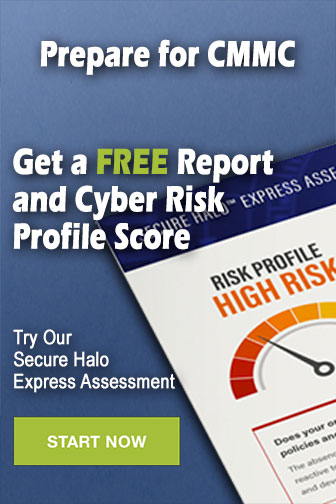