1-21
voltage induced in one stator winding cannot be measured because the common connection between the
stator coils is not physically accessible.
In summary, the synchro transmitter converts the angular position of its rotor into electrical stator
signals, which are sent through interconnecting wires to other synchro devices.
Q-20. When is the maximum voltage induced into a stator coil?
Q-21. What three factors determine the amplitude of the voltage induced into a stator winding?
SYNCHRO TORQUE RECEIVER
Synchro torque receivers, commonly called synchro receivers, are electrically identical to torque
transmitters of the same size except for the addition of some form of damping. In some sizes of 400-Hz
synchros, units are designated as torque receivers but may be used as either transmitters or receivers.
Unlike the transmitter, the receiver has an electrical input to its stator and a mechanical output from
its rotor. The synchro receiver's function is to convert the electrical data supplied to its stator from the
transmitter, back to a mechanical angular position through the movement of its rotor. This function is
accomplished when the rotor is connected to the same ac source as the transmitter and assumes a position
determined by the interaction of its magnetic field with the magnetic field of the stator. If you recall, this
is the same concept discussed earlier under the operation of electromagnets.
Normally, the receiver rotor is unrestrained in movement except for brush and bearing friction.
When power is first applied to a system, the transmitter position changes quickly; or if the receiver is
switched into the system, the receiver rotor turns to correspond to the position of the transmitter rotor.
This sudden motion can cause the rotor to oscillate (swing back and forth) around the synchronous
position If the movement of the rotor is great enough, it may even spin. Some method of preventing
oscillations or spinning must be used. Any method that accomplishes this task is termed DAMPING.
There are two types of damping methods ELECTRICAL and MECHANICAL. In small synchros the
electrical method is used more frequently than the mechanical method. This method uses an additional
winding placed in the synchro to retard oscillations. In larger units, a mechanical device, known as an
inertia damper, is more effective. Several variations of the inertia damper are in use. One of the more
common types consists of a heavy brass flywheel (inertia damper), which is free to rotate around a
bushing that is attached to the rotor shaft (fig. 1-15). A tension spring on the bushing rubs against the
flywheel so that the bushing and flywheel turn together during normal operation. If the rotor shaft turns or
tends to change its speed or direction of rotation suddenly, the inertia of the damper opposes the changing
condition.
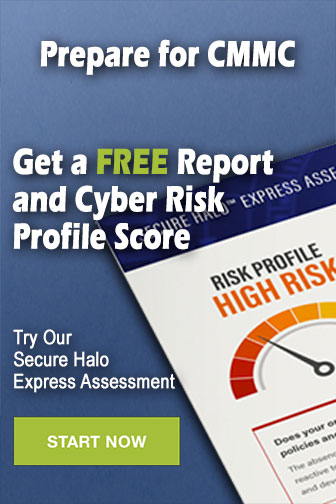