1-33
In this figure the signal from TX No. 1 rotates the resultant TDR stator field 75º counterclockwise. In
a similar manner, the signal from TX No. 2 rotates the resultant TDR rotor field counterclockwise 30º.
Since the two resultant fields are not rotated by equal amounts, a torque is exerted on the rotor to bring
the two fields into alignment. This torque causes the rotor to turn to 45º, the point at which the two fields
are aligned. To bring the two fields into alignment, the TDR rotor need turn only through an angle equal
to the difference between the signals supplied by the two TXs.
TX-TDR-TX System Operation (Addition)
To set up the previous system for addition, it is necessary to reverse only the R1 and R3 leads
between the TDR rotor and TX No. 2. With these connections reversed, the system operates as shown in
figure 1-23.
Figure 1-23.TX-TDR-TX system operation (addition).
Assume the TDR rotor is initially at 0º. TX No. 1 is turned to 75º, and TX rotor No. 2 is turned to
30º. The TDR stator field still rotates counterclockwise 75º, but because R1 and R3 on the TDR rotor are
reversed, its rotor field rotates 30º clockwise. The angular displacement of the two fields then, with
respect to each other, is the sum of the signals transmitted by the two TXs. The magnetic force pulling the
TDR rotor field into alignment with that of the stator turns the TDR rotor to 105º. Therefore, the system
solves the equation 75º + 30º = 105º.
Q-38. What connections in a TDR system are reversed to set up the system for addition?
Q-39. In a TDR system connected for addition in what direction will the TDR rotor field turn when the
TX rotor to which it is connected turns counterclockwise?
CONTROL SYNCHRO SYSTEMS
It should be clear to you from our discussion of torque synchro systems that, since they produce a
relatively small mechanical output, they are suitable only for very light loads. Even when the torque
system is moderately loaded, it is never entirely accurate because the receiver rotor requires a slight
amount of torque to overcome its static friction.
When large amounts of power and a higher degree of accuracy are required, as in the movement of
heavy radar antennas and gun turrets, torque synchro systems give way to the use of CONTROL
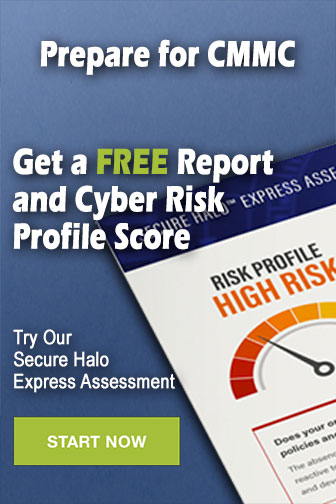