2-4
Figure 2-2B.A basic servo system (closed-loop).
Figure 2-2C.A basic servo system (closed-loop).
Figure 2-2D.A basic servo system (closed-loop).
The synchro-control system provides a means of controlling the movement of the load, which may
be located in a remote space. The servo amplifier and servo motor are the parts of the system in which
power is actually developed (to move the load).
As you remember, the controlling signal from a CT is relatively weak, too weak to drive an electric
motor directly. In views A through D of figure 2-2, assume that the control signal will be initiated by a
handcrank input connected to the synchro transmitter (CX). The dials located on the CX and the CT
indicate the positions of the synchro's rotors, while the dial on the load indicates the position of the load.
In view A, the dials of both the CX and the load indicate that the load is in the desired position.
Because the load is where it should be, there will be no error signal present at the servo amplifier and no
power to the servo motor.
In view B, the rotor of the CX has been moved by the handcrank to 90º. (This indicates that it is
ordered to move the load by 90º.) Notice that the rotor of the CT is still at 0º. The CT now develops a
signal, called the ERROR SIGNAL, which is proportional in amplitude to the amount the CT rotor is out
of correspondence with the CX rotor. The phase of the error signal indicates the direction the CT rotor
must move to reduce the error signal to zero or to "null out." The error signal is sent to the servo
amplifier. In view C, the error signal has been amplified by the servo amplifier and sent on to the servo
motor. The motor starts to drive in the direction that will reduce the error signal and bring the CT rotor
back to the point of correspondence. In this case the motor is turning clockwise.
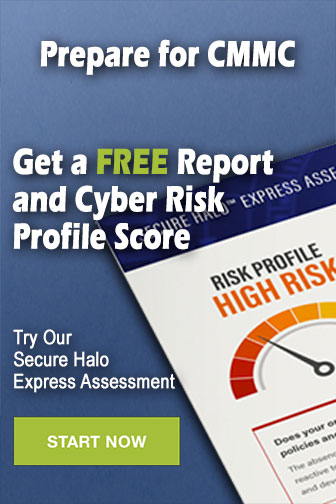