2-25
Figure 2-25.Dip-tinning In a solder pot.
The flux used in tinning copper wire is a mixture of denatured alcohol and freshly ground rosin. This
type of flux may be mixed just prior to use. A premixed paste flux may also be used. The solder used for
terminal lugs, splices, and connectors is a mixture of 60-percent tin and 40-percent lead. Maintain the
temperature of the solder bath (pot) between 450 and 500º
F. This keeps the solder in a liquid state. Skim
the surface of the solder pot, as necessary, with a metal spoon or blade. This keeps the solder clean and
free from oxides, dirt, and so forth.
Dip-tin wires smaller than No. 8 in groups of 8 or 10. Dip-tin wires size No. 8 and larger
individually. The procedure for dip-tinning is as follows:
1. Prepare the flux and solder as previously described.
2. Make sure the exposed end of the wire is clean and free from oil, grease, and dirt. Strands should
be straight and parallel. Dirty wire should be restripped.
3. Grasp the wire firmly and dip it into the prepared flux to a depth of about 1/8 inch (see view A of
figure 2-25).
4. Remove the wire and shake off the excess flux.
5. Immediately dip the wire into molten solder. Dip only half of the stripped conductor length into
the solder (see view B of figure 2-25).
6. Turn the wire slowly in the solder bath until the wire is well tinned. Watch the solder fuse to the
wire. Do not keep the wire in the bath longer than necessary.
7. Remove the excess solder by wiping the tinned conductor on a cloth.
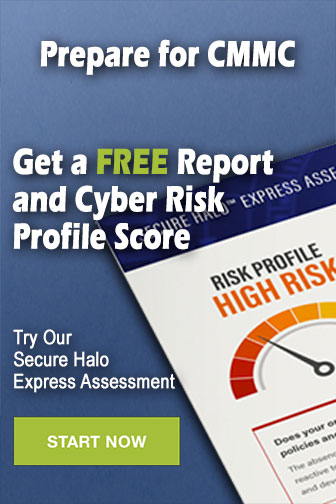