2-23
Figure 2-24.Locating splice in crimping tool.
3. Squeeze the tool handles slowly until the tool jaws hold the spice barrel firmly in place, but
without denting he barrel.
4. Insert the stripped wire into the splice barrel, which protrudes from the "wire side" of the splice,
until the stripped end of wire butts against the stop in the center of the splice. This can be seen
through the splice inspection window.
5. Crimp by closing the tool handles. The tool will not open until the full crimping cycle has been
completed.
6. After crimping, check that the wire end is still visible through the splice inspection window.
7. Reverse the position of the splice in the crimping tool (or location of the crimping tool on the
splice) and repeat steps 1 through 6 to crimp the wire into the other side of the splice.
If the correct tools are used and the proper procedures followed, crimp-on connections are more
effective electrically, as well as mechanically, than soldered connections. A visual inspection is very
important. It reveals oxidation, deterioration, overheating, and broken conductors. In some cases it may
be necessary to check these connections with an ohmmeter. The proper resistance, for all practical
purposes, should be zero. Any defective terminal should be removed and a new terminal crimped on.
Q18.
What is the most common method of terminating and splicing wires?
Q19.
Besides not having to insulate a noninsulated terminal, what other advantage is gained by using
a preinsulated terminal lug?
Q20.
Why are preinsulated terminal lugs and splices color coded?
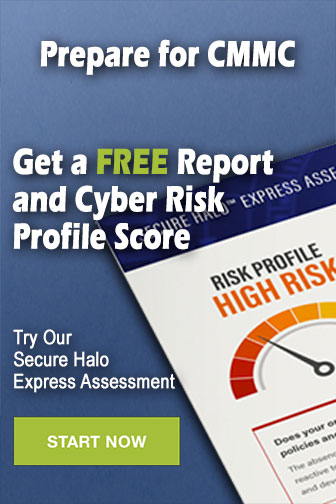