2-20
other than eutectic, go through a plastic or semiliquid state in their heating and cooling stages. Solder
joints that are disturbed (moved) during the plastic state will result in damaged connections. For this
reason, 63/37 solder is the best alloy for electronic work. Solder with 60/40 alloy is also acceptable, but it
goes into a plastic state between 361 and 370 degrees Fahrenheit. When soldering joints with 60/40 alloy,
you must exercise extreme care to prevent movement of the component during cooling.
USE OF FLUX IN SOLDER BONDING
Reliable solder connections can only be accomplished with clean surfaces. Using solvents and
abrasives to clean the surfaces to be soldered is essential if you are to achieve good solder connections. In
almost all cases, however, this cleaning process is insufficient because oxides form rapidly on heated
metal surfaces. The rapid formation of oxides creates a nonmetallic film that prevents solder from
contacting the metal. Good metal-to-metal contact must be obtained before good soldering joints may
take place. Flux removes these surface oxides from metals to be soldered and keeps them removed during
the soldering operation. Flux chemically breaks down surface oxides and causes the oxide film to loosen
and break free from the metals being soldered.
Soldering fluxes are divided into three classifications or groups: CHLORIDE FLUX (commonly
called ACID), ORGANIC FLUX, and ROSIN FLUX. Each flux has characteristics specific to its own
group. Chloride fluxes are the most active of the three groups. They are effective on all common metals
except aluminum and magnesium. Chloride fluxes, however, are NOT suitable for electronic soldering
because they are highly corrosive, electrically conductive, and are difficult to remove from the soldered
joint.
Organic fluxes are nearly as active as chloride fluxes, yet are less corrosive and easier to remove
than chloride fluxes. Also, these fluxes are NOT satisfactory for electronic soldering because they must
be removed completely to prevent corrosion.
Rosin fluxes ARE ideally suited to electronic soldering because of their molecular structure. The
most common flux used in electronic soldering is a solution of pure rosin dissolved in suitable solvent.
This solution works well with the tin- or solder-dipped metals commonly used for wires, lugs, and
connectors. While inert at normal temperatures, rosin fluxes break down and become highly active at
soldering temperatures. In addition, rosin is nonconductive.
Most electronic solder, in wire form, is made with one or more cores of rosin flux. When the joint or
connection is heated and the wire solder is applied to the joint (not the iron), the flux flows onto the
surface of the joint and removes the oxide. This process aids the wetting action of the solder. With enough
heat the solder flows and replaces the flux. Insufficient heat results in a poor connection because the
solder does not replace the flux.
Q10. Stereoscopic-zoom microscopes and precision drill presses are normally associated with what
type of repair station?
Q11. Solder used in electronic repair is normally an alloy of what two elements?
Q12. In soldering, what alloy changes directly from a solid state to a liquid state?
Q13. Flux aids in soldering by removing what from surfaces to be soldered?
Q14. What type(s) of flux should never be used on electronic equipment?
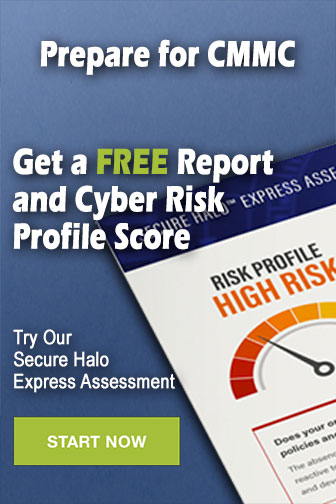