2-19
found in closed ventilation systems. This need is particularly important aboard ship. Vented hoods, ducts,
or installations that are vented outside generally meet the minimum standards set by the Naval
Environmental Health Center.
NOISE CONSIDERATIONS
Noise in the work area during normal work periods must be no greater than the acceptable level
approved for each activity involved. Because the work is tedious and tiring, noise levels should be as low
as possible. Ear protectors are required to be worn when a noise level exceeds 85 dB. Ear protectors
should also be worn anytime the technician feels distracted by, or uncomfortable with, the noise level.
WORK SURFACE AREA
Work stations should have a minimum work surface of at least 60-inches wide and 30-inches deep.
Standard Navy desks are excellent for this purpose. Standard shipboard workbenches are acceptable;
however, off-white or pastel-colored heat-resistant tops should be installed on the workbenches. Chairs
should be the type with backs and without arms. They should be comfortably padded and of the proper
height to match the work surface height. Drawers or other suitable tool storage areas are usually provided.
ELECTROSTATIC DISCHARGE SENSITIVE DEVICE (ESDS) CAPABILITY
A 2M work station should be capable of becoming a static-free work station. This is specified in the
Department of Defense Standard, Electrostatic DISCHARGE Control Program for Protection of Electrical
and Electronic Parts, Assemblies, and Equipment. ESD will be discussed in greater detail in topic 3.
POWER REQUIREMENTS
No special power source or equipment mounting is required. The 2M repair equipment operates on
115-volt, 60-hertz power. A 15-ampere circuit is sufficient and six individual power receptacles should be
available.
HIGH-RELIABILITY SOLDERING
The most common types of miniature and microminiature repair involve the removal and
replacement of circuit components. The key to these repairs is a firm knowledge of solder and high-
reliability soldering techniques.
Solder is a metal alloy used to join two or more metals with a metallic bond. The bonding occurs
when molten solder dissolves a small amount of the metals and then cools to form a solid connection. The
solder most commonly used in electronic assemblies is an alloy of tin and lead. Tin-lead alloys are
identified by their percentage in the solder; the tin content is given first. Solder marked 60/40 is an alloy
of 60 percent tin and 40 percent lead. The two most common alloys used in electronics are 60/40 and
63/37.
The melting temperature of tin-lead solder varies depending on the percentage of each metal. Lead
melts at a temperature of 621 degrees Fahrenheit, and tin melts at 450 degrees Fahrenheit. Combinations
of the two metals melt into a liquid at different temperatures. The 63/37 combination melts into a liquid at
361 degrees Fahrenheit. At this temperature, the alloy changes from a solid directly to a liquid with no
plastic or semiliquid state. An alloy with such a sharp changing point is called a EUTECTIC ALLOY.
As the percentages of tin and lead are varied, the melting temperature increases. Alloy of 60/40 melts
at 370 degrees Fahrenheit, and alloy of 70/30 melts at approximately 380 degrees Fahrenheit. Alloys,
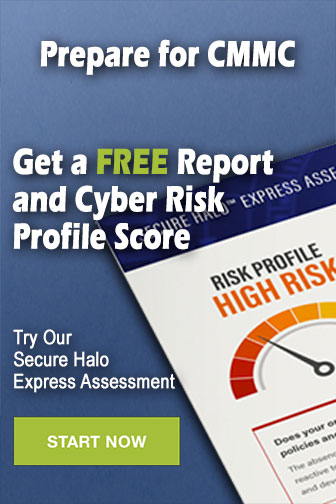