1-23
Dual Inline Package
The dual inline package (DIP) was designed primarily to overcome the difficulties associated with
handling and inserting packages into mounting boards. DIPs are easily inserted by hand or machine and
require no spreaders, spacers, insulators, or lead-forming tools. Standard hand tools and soldering irons
can be used to field-service the devices. Plastic DIPs are finding wide use in commercial applications, and
a number of military systems are incorporating ceramic DIPS.
The progressive stages in the assembly of a ceramic DIP are illustrated in figure 1-24, views (A)
through (E). The integrated-circuit die is sandwiched between the two ceramic elements, as shown in
view (A). The element on the left of view (A) is the bottom half of the sandwich and will hold the
integrated-circuit die. The ceramic section on the right is the top of the sandwich. The large well in view
(B) protects the IC die from mechanical stress during sealing operations. Each of the ceramic elements is
coated with glass which has a low melting temperature for subsequent joining and sealing. View (B)
shows the Kovar lead frame stamped and bent into its final shape. The excess material is intended to
preserve pin alignment. The holes at each end are for the keying jig used in the final sealing operation.
The lower half of the ceramic package is inserted into the lead frame shown in view (C). The die is
mounted in the well and leads are attached. The top ceramic elements are bonded to the bottom element
shown in view (D) and the excess material is removed from the package. View (E) is the final product.
Figure 1-24.DIP packaging steps.
Ceramic DIPs are processed individually while plastic DIPs are processed in quantities of two or
more (in chain fashion). After processing, the packages are sawed apart. The plastic package also uses a
Kovar lead frame, but the leads are not bent until the package is completed. Because molded plastic is
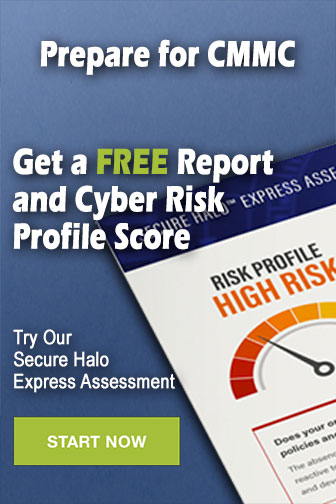