4-53
in all spaces where electronic equipment is present. Therefore, before starting to work on any electronic
or electrical equipment, ALWAYS ENSURE THAT THE EQUIPMENT AND ANY TEST
EQUIPMENT YOU ARE USING IS PROPERLY GROUNDED AND THAT THE RUBBER MAT
YOU ARE STANDING ON IS IN GOOD CONDITION. As long as you follow these simple rules, you
should be able to avoid the possibility of becoming an electrical conductor.
TESTING
There are two widely used checks in testing electronic equipment, VISUAL and SIGNAL
TRACING. The importance of the visual check should not be underestimated because many technicians
find defects right away simply by looking for them. A visual check does not take long. In fact, you should
be able to see the problem readily if it is the type of problem that can be seen. You should learn the
following procedure. You could find yourself using it quite often. This procedure is not only for power
supplies but also for any type of electronic equipment you may be troubleshooting. (Because diode and
transistor testing was covered in chapter 1 and 2 of this module, it will not be discussed at this time. If
you have problems in this area, refer to chapter 1 for diodes or chapter 2 for transistors.)
1. BEFORE YOU ENERGIZE THE EQUIPMENT, LOOK FOR:
a. SHORTSAny terminal or connection that is close to the chassis or to any other terminal
should be examined for the possibility of a short. A short in any part of the power supply can
cause considerable damage. Look for and remove any stray drops of solder, bits of wire,
nuts, or screws. It sometimes helps to shake the chassis and listen for any tell-tale rattles.
Remember to correct any problem that may cause a short circuit; if it is not causing trouble
now, it may cause problems in the future.
b. DISCOLORED OR LEAKING TRANSFORMERThis is a sure sign that there is a short
somewhere. Locate it. If the equipment has a fuse, find out why the fuse did not blow; too
large a size may have been installed, or there may be a short across the fuse holder.
c. LOOSE, BROKEN, OR CORRODED CONNECTIONAny connection that is not in good
condition is a trouble spot. If it is not causing trouble now, it will probably cause problems in
the future. Fix it.
d. DAMAGED RESISTORS OR CAPACITORSA resistor that is discolored or charred has
been subjected to an overload. An electrolytic capacitor will show a whitish deposit at the
seal around the terminals. Check for a short whenever you notice a damaged resistor or a
damaged capacitor. If there is no short, the trouble may be that the power supply has been
overloaded in some way. Make a note to replace the part after signal tracing. There is no
sense in risking a new part until the trouble has been located.
2. ENERGIZE THE EQUIPMENT AND LOOK FOR:
a. SMOKING PARTSIf any part smokes or if you hear any boiling or sputtering sounds,
remove the power immediately. There is a short circuit somewhere that you have missed in
your first inspection. Use any ohmmeter to check the part once again. Start in the
neighborhood of the smoking part.
b. SPARKINGTap or shake the chassis. If you see or hear sparking, you have located a loose
connection or a short. Check and repair.
If you locate and repair any of the defects listed under the visual check, make a note of what you find
and what you do to correct it. It is quite probable you have found the trouble. However, a good technician
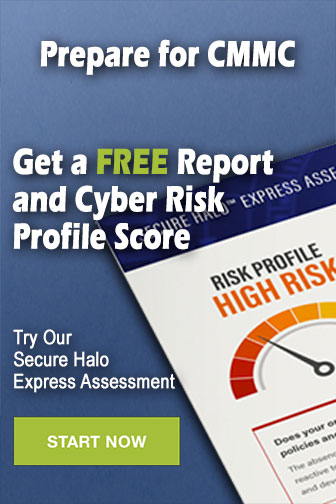