3-5
physically contact the workpiece surface. Delicate work handled in this manner permits you to observe
the removal process.
Figure 3-2.Hot air jet conformal coating removal.
POWER-TOOL REMOVAL DESCRIPTION.Power-tool removal is the use of abrasive
grinding or cutting to mechanically remove coatings. Abrasive grinding/rubbing techniques are effective
on thin coatings (less than 0.025 inch) while abrasive cutting methods are effective on coatings greater
than 0.025 inch. This method permits consistent and precise removal of coatings without mechanical
damage or dangerous heating to electronic components. A variable-speed mechanical drive handpiece
permits fingertip-control and proper speed and torque to ease the handling of gum-type coatings. A
variety of rotary abrasive materials and cutting tools is required for removal of the various coating types.
These specially designed tools include BALL MILLS, BURRS, and ROTARY BRUSHES.
The ball mill design places the most efficient cutting area on the side of the ball rather than at the
end. Different mill sizes are used to enter small areas where thick coatings need to be removed
(ROUTED). Rubberized abrasives of the proper grade and grit are ideally suited for removing thin, hard
coatings from flat surfaces; soft coatings adhere to and coat the abrasive causing it to become ineffective.
Rotary bristle brushes work better than rubberized abrasives on contoured or irregular surfaces, such as
soldered connections, because the bristles conform to surface irregularities. Ball mill routing and abrasion
removal are shown in figure 3-3.
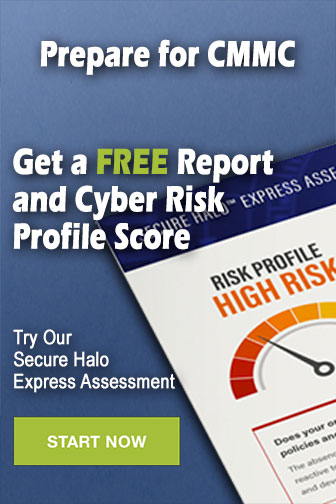