1-7
used to cover adjustments or controls that are part of the normal use and operation of the instrument. This
label may also be used to prevent removal and/or interchange of plug-ins, modules, subassemblies, and so
forth, when such removal or interchange would affect the calibration.
REPAIR PROCEDURES
If you are unable to replace a known failed component with onboard spares, you can often locate the
replacement component from other supply sources. The replacement component can then be delivered,
along with the inoperative equipment, to the IMA. So by sending the repair part along with the
equipment, you can reduce repair time considerably. This is particularly true when your unit is getting
under way and no time is available for you to complete the repair before calibration. Most operational
commands have a higher supply priority for purchase of repair parts than the IMA can use.
"No Reject" Policy
IMAs have a "no reject" policy on test equipment to provide operational test equipment in a more
timely manner. The "no reject" policy says, in effect, that test equipment submitted to the IMA for
calibration, which is later found to require repair, will be repaired by the repair department of the IMA.
Before this policy, any equipment found inoperative by the calibration lab was marked REJECTED, the
reasons stated, and the equipment returned uncalibrated to the ship for repairs. The "no reject" policy does
not relieve you of your responsibility to ensure your equipment is in working order prior to submitting it
for calibration. Its purpose is to streamline the procedure and cut down delays in returning your
equipment to you calibrated and ready to use.
Responsibility for Repair and Maintenance of Test Equipment
Generally, the responsibility for repair and maintenance of test equipment is placed on maintenance
personnel. In some cases, however, maintenance personnel are not authorized to make repairs. Then the
test instrument must be sent to a shore repair/calibration facility.
Q-7. Responsibility for repair and maintenance of test equipment generally rests with what group of
personnel?
When test equipment is sent for calibration and repair, all accessories, such as probes, adapters, and
calibration sheets, should be included. Only in emergencies or special situations should partial repair or
calibration be attempted on test equipment designated as nonrepairable. Such emergency repairs should
be noted on a tag attached to the unit and an entry made on the MEASURE card (discussed shortly). The
equipment should then be sent at the earliest opportunity to an authorized facility so that permanent
repairs can be made and the unit calibrated.
STOWAGE AND HANDLING OF TEST EQUIPMENT
Most electronic test equipment is precision equipment. Such equipment must be handled with care to
properly perform its designed functions. Rough handling, excessive heat, moisture, and dust all affect the
useful life of the equipment. Bumping or dropping a test instrument may ruin the calibration of a meter,
cause short circuits, or damage electronic elements inside the case. Sharp bends, creases, or dents in
coaxial test cables can alter the expected attenuating effect and cause false meter readings or
measurements. Forced air cooling, dust filters, and heaters are used in many pieces of equipment. This
test equipment requires clean air filters for proper ventilation and a warm-up period that permits units in
the equipment to maintain calibrated standards.
Electronic test equipment should be stowed in a dry location with the dust cover (if provided) in
place. Dust covers for spare plug-in units should be constructed for such stowage. For ease in performing
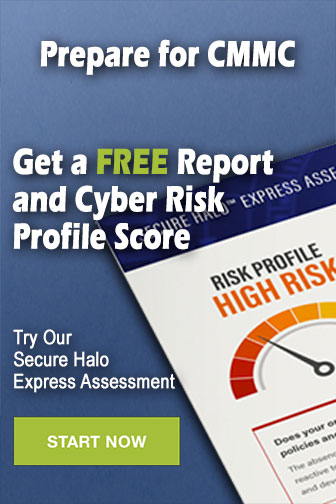